Cattani Equipment Installation
What You Need to Know
Suction and air supply are the unsung heroes of the dental practice. Without their optimal performance and reliability, work suffers and can even stop, so it is essential that your Cattani equipment is installed correctly.
Your Cattani dealer will discuss with you the various installation options and recommend those that best suit your clinic and environment. The information below is a useful starting point for site requirements, while your installer has the expertise to ensure your set-up produces optimal performance and longevity.
The team at Cattani is also happy to advise you on planning your installation.
Call us at +61 3 9484 1120.
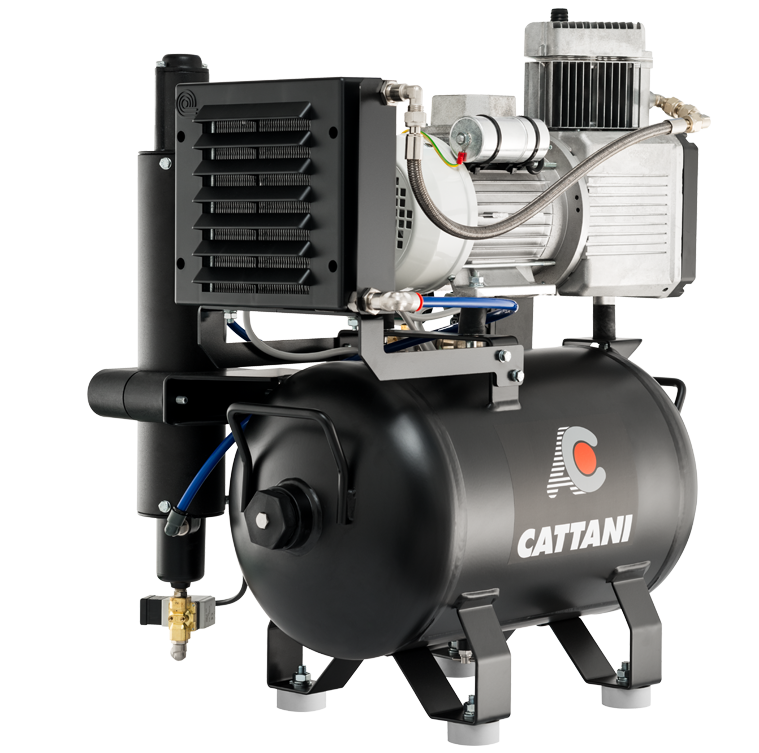
Suction System Essentials
The suction piping system uses DWV PVC pipe and connects each dental surgery back to the suction unit in the plant room. The suction unit should be installed on the same floor level or below the level of the dental chairs. It should have a constant fall from the chairs towards the suction unit and cannot include 90° junctions, dips, U-shapes or rises. Termination within the dental surgery is typically at the floor junction box of the dental chair, but is site dependent. The chair manufacturer or installer should be consulted for location details.
Your suction unit will need:
• Suction inlet connection – termination of suction piping that connects to dental surgeries
• Waste connection – sewer drain pipe terminated lower than waste outlet of suction unit
• Exhaust air outlet connection – piping that directs exhaust air to atmosphere outside the building
• Power supply – dedicated electrical power circuit to run the suction unit
• Control switch wiring – switch wiring to connect the dental surgeries to the suction unit
View our range of Suction Systems
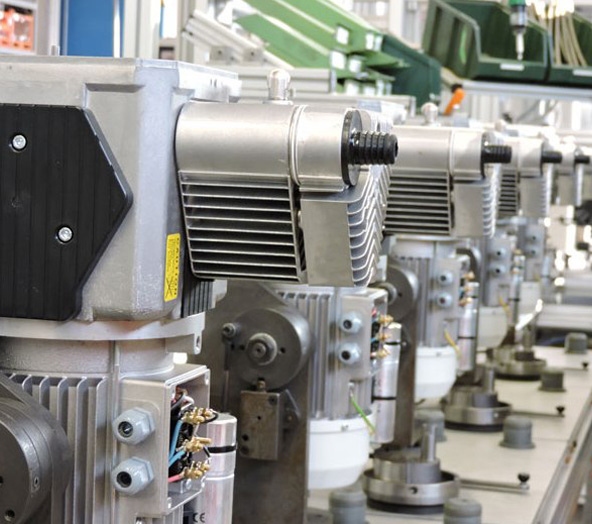
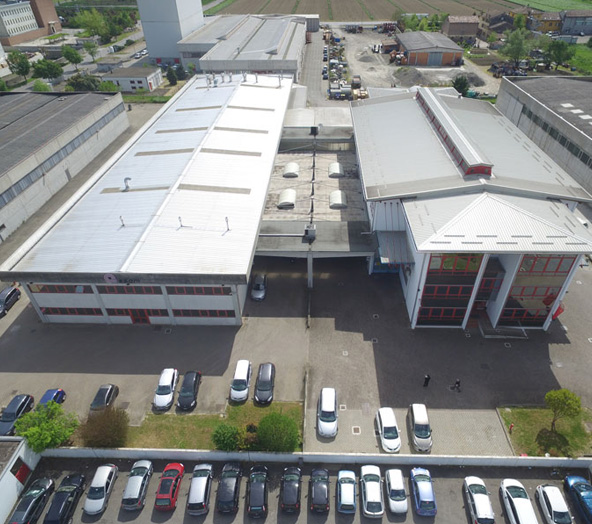
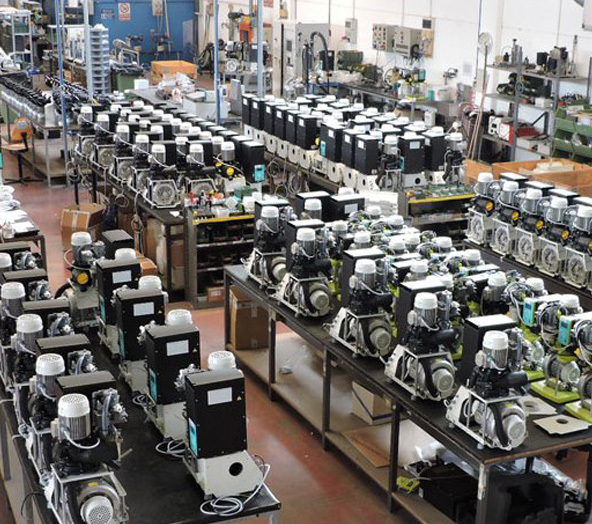
Compressor Essentials
The compressed air piping system is typically copper and connects each dental surgery back to the compressor unit in the plant room. Termination within the dental surgery is typically at the floor junction box of the dental chair, but is site dependent. The chair manufacturer or installer should be consulted for location details.
Your compressor will need:
• Compressed air outlet connection – termination of compressed air piping system that connects to the dental surgeries
• Power supply – dedicated electrical power circuit to run the suction unit
• Waste connection (optional) – sewer connection to allow drainage of compressor condensate
View our range of Compressors
Location and Access – Where to Position Your Plant Room
When designing a new practice, the location of your plant room is an important consideration because proper planning will ensure the most efficient and balanced suction performance. Locating the plant room close to surgeries prevents under-performance caused by excessive pipeline lengths. The plant room must be on the same floor as the dental chairs, or below them. Fluids need to fall to the pump, so if there is a floor below the chairs, like a car park or basement that is accessible and still close to the dental suites above, that location would be ideal for the plant room. Many sites also have air-conditioned plant rooms to protect their investment.
Maximise Your System’s Performance with an Air Injector Valve
Cattani highly recommends the use of an Air Injector Valve with all suction systems. It is best to install one at the time the clinic is constructed but they can also be added later.
Air must flow through the piping in a suction system to help aspirated fluids reach the suction unit. Depending on the site scenario, it is possible that insufficient air will flow through the system. This can lead to fluctuations in performance as fluids pool at the lowest part of the system, with air flow falling below optimal levels. An Air Injector Valve, installed at the end of the pipeline, is an excellent way to compensate for any lack of air volume.
There are two types available:
• Standard Air Injector Valve – a constantly variable unit that allows the flow of small volumes of air over long periods. It is a simple spring-loaded, vacuum-actuated valve, designed to open at the same time that the chairs are in operation.
• Automatic Air Injector Valve – an automated unit that allows the flow of large volumes of air over short periods. This is an electro-pneumatic valve that is actuated by an electrical signal. It is designed to open only when all chairs have ceased operation. With no air flow required from the chairs, the valve allows a large volume of air to be injected into the system without compromising the performance to the chair.
If you are building a new clinic, we strongly recommend that you make provision for an Air Injector Valve to be fitted, even if you don’t install it straight away. It is much simpler to install an Air Injector Valve to existing services rather than have to add those services later. To provide for an Air Injector Valve, you need to extend the suction pipeline past the chair furthest from the suction unit, terminating the line at a point higher than the main suction pipe line, in an accessible area like a cabinet, ceiling space, void etc. An additional switch cable between this point and the suction unit is also required. Ensure that the pipe is capped if an Air Injector Valve is not being installed immediately. If a system does not have the extra pipe-work from the start, an Air Injector Valve can be retro-fitted by adding it to the floor junction box of the dental chair. However, the noise generated by the aspirated air can be disruptive.
Pipeline Design and Layout
The pipeline needs to facilitate the flow of air and fluids back to the plant room. Pipelines should be designed with a main pipe connected to branches from each dental chair. Large clinics may also require sub-branches. Where possible the piping should take the shortest and straightest route between the plant room and the last dental chair on the line. The diameter of the pipe depends on the number of chairs and the proximity to the plant room: in simple terms, the further from the plant room, the smaller the pipe.
Pipe Size Guidelines
Pipe size plays a crucial role in ensuring an even air flow and efficient evacuation of fluids. Suction plumbing requirements based on an the average air flow rate of 350l/min per chair are:
• 1-2 chairs – 40mm DWV pipe
• 3-6 chairs – 50mm DWV pipe
• 7-10 chairs – 65mm DWV pipe
• 11-15 chairs – 80mm DWV pipe
Pipeline Configuration Guidelines
Bends in the pipeline should never be greater than 45°. If a 90° bend is required, use 2 x 45° bends together in-line. All branches entering a main line must use 45° junctions. Do not use a T-junction when splitting main lines into two branches. Instead, use a 45° Y-junction for the first branch off the main line and 2 x 45° bends for the second.
Pipeline Rise and Fall Guidelines
The pipeline should slope constantly towards the suction unit in the plant room. Strictly avoid dips and U-shapes around beams etc to prevent fluids pooling at the lowest point and restricting air flow. If the suction unit is installed on the same floor as the dental chairs, a single vertical rise should be installed just before the unit with the height kept to a minimum. The higher this rise, the greater the risk of fluids creating a wave effect as they try to reach the inlet of the suction unit. This “wave” may cause fluctuating performance at the suction tips.
Ventilation Guidelines – Controlling the Temperature in Your Plant Room
Air Conditioning
Air conditioning is the best way to maintain the stable temperatures your plant room equipment needs for optimal performance. Modern split systems are the most efficient and affordable. And with a dedicated air conditioner in your plant room, no vents are required, so noise emissions are greatly reduced.
The clinic’s central air conditioning system must not include the plant room. Instead the room should have its own dedicated air conditioner. Central systems are designed for human comfort and the thermostat is usually located in reception. It cannot sense the temperature in the plant room, so in winter, for example, it would often be heating the room, even though it generates its own heat.
Recommendations for plant room air conditioning:
• 1-4 surgeries – 2.5 kW
• 6-8 surgeries – 4.5 kW
• 4-6 surgeries – 3.5 kW
• 8-10 surgeries – 5.5 kW
Fan-forced Ventilation
Fan-forced ventilation systems turn over the air in the plant room. Cool air is drawn in while hot air is exhausted via the in-line fan. With this ventilation method we recommend a fan capacity of 100m3/hr per 1 kW power rating of your equipment.
There are drawbacks with fan-forced ventilation:
• Noise – the vents needed to allow air to flow through the plant room also allow more noise to escape the room, including extra noise generated by the cooling fans.
• Temperature – an efficient fan-forced ventilation system will only reduce the temperature to 10°C above the incoming air temperature. Also, temperature control is only as consistent as the incoming air temperature.
Noise Reduction Options
All plant room equipment generates noise, which can irritate dentists, staff and patients. The noise level may also breach council and body corporate regulations. Any noise reduction solution that will cause equipment to overheat is out of the question, so a balance between ventilation and noise reduction needs to be found:
• The plant space can be air conditioned to eliminate the need for vents
• The space may be lined with sound-deadening material
• Cattani supplies Acoustic Covers for certain models
• Mufflers can be fitted to the suction exhaust outlet
• Fan-forced ventilation vents can be baffled (see below)
A simple baffle can reduce noise escaping from vents. Essentially, a box with one end open is placed over the vent. Air can pass through but noise is absorbed. The box can be made of materials similar to cabinet doors and ideally should be lined with sound-deadening material. Ensure that the open end of the box is large enough so that it does not restrict air flow. Restricting air flow will compromise the efficiency of the ventilation system.