This is a suction system
200-chair Cattani installation at Sydney Dental Hospital
If you are reading this, you probably already know the size of the suction unit that manages a single dental chair. But can you picture the “unit” that runs 200 chairs? To save you the trouble, we’re showing it to you here. This is the recently commissioned Cattani suction system that serves Sydney Dental Hospital.
Quality comes first but size is no object with Cattani
The Sydney hospital installation has been an epic, 18-month project, from first consultation to completion. Cattani Technical Manager Mark Humphries, who played a key role in the design and installation of the system, says:
“With a project of this size, quality is paramount but it is in fact the size that stands out more than anything.
Everything about it is huge – the piping, the separators, the HEPA filters – you name it. Even transportation of the equipment from Italy wasn’t easy, and then the installation involved finding solutions to big logistical issues within the hospital.
The project is part of a much larger redevelopment in which all of the hospital’s chairs are being converted from an old and inefficient dry suction system to semi-wet. The refurbishment and chair replacement programme has now started. All 200 chairs will be upgraded and converted in stages, with Cattani’s suction system now serving both the old dry suction chairs and the new semi-wet ones as and when they are installed.
For Cattani, the project started in May 2016 when Business Development Manager Jason Borg met hospital engineers and immediately saw that he could dramatically improve on their plan. He followed up with a detailed proposal that replaced the hospital’s piecemeal and staged suction system conversion strategy with a “bite the bullet” alternative that had the whole thing done in one go, while saving them hundreds of thousands of dollars and valuable floor space.
The key thing is that we worked with the client, offering multiple solutions as well as our expertise and background information so that they could make the right decision for them,” said Jason.
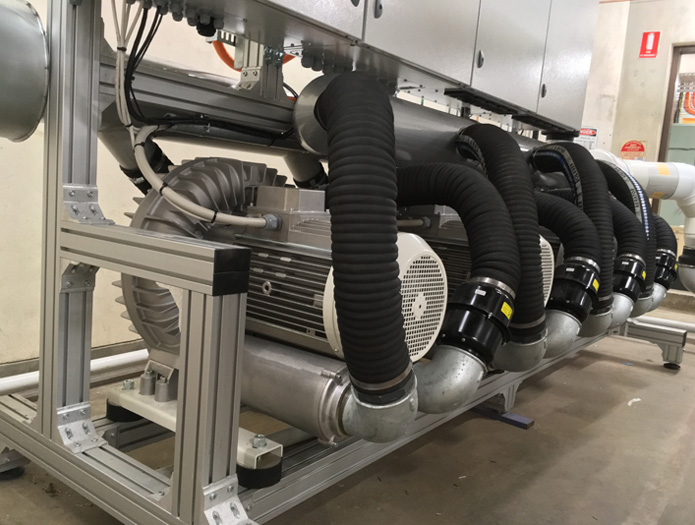
Bespoke variable speed Blok-Jet system with back-up
Once the plan was accepted, the project team had to find a suitable location in the hospital for the large-scale, hi-tech plant equipment (in the basement), then actually design the system, and then work out how to plumb it through the labyrinthine building. The result, completed in collaboration with the project’s major engineering contractor Hoslab, is a unique, bespoke Blok Jet system with variable speed (using Cattani inverter control technology), with back-up, separator tanks and drain pumps, that will serve all of the hospital’s chairs for many years to come. For the record, the system is a Cattani Blok Jet 4 x Uni Jet 1000 with four 20KW inverters.
The piping network through the hospital resembles a tree, with the initial riser a trunk-like 300mm pipe that branches into successively smaller pipes as they spread through the hospital. Two 2.2-metre tall separator tanks, receive the aspirated fluid. Each of these separators is itself drained by a Cattani Turbo SMART B unit with a Hydrocyclone amalgam separator (there are four Turbo SMART B’s in total – two for each separator tank). The separated air passes through HEPA filters the size of oil drums, and the then breathable air leaves the building as exhaust.
Jason and Mark and their Cattani Australia colleagues had to come up with unique design solutions to achieve optimal operational performance and efficiency, and the size of the system components presented their own challenges. Thirteen crates, two of them each the size and weight of a small truck, were carried on semi-trailers from the Cattani factory in Parma, Italy to Schiphol Airport in Holland where they sat until a freight plane large enough was available to fly them to Sydney. “It’s not just the size but also the height,” said Mark. “It was like transporting a giraffe.”
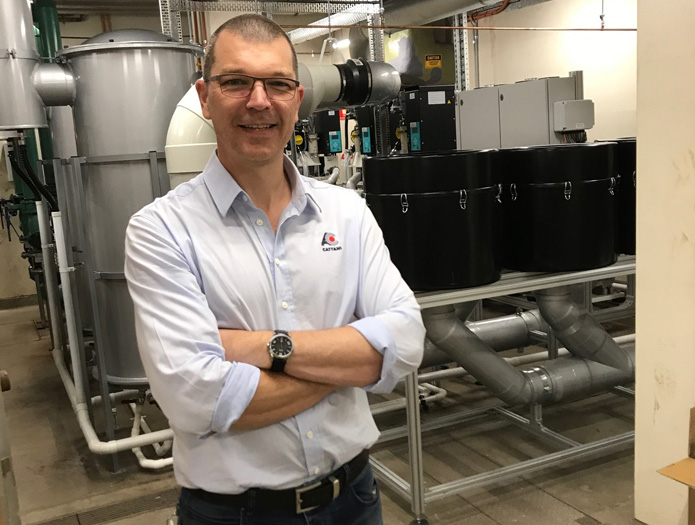
Installation a complex operation
Once in Sydney, the crates were transported to the dental hospital, which is next to Central Station in the heart of the city, along a carefully scoped out route that could take such a high load. With traffic diverted, the crates were then lifted by crane into the hospital basement, but only after the two floors above had been removed to make that manoeuvre possible. A month later, the system was installed and running.
For scale and complexity, few things match this project in Cattani’s history, and we’re proud of Jason and Mark, and everyone else here who contributed to its successful completion.
OTHER STORIES